以下是針對石油石化行業噪聲治理的系統性總結與分析,基于噪聲源特征、治理方案及工程難點梳理而成:
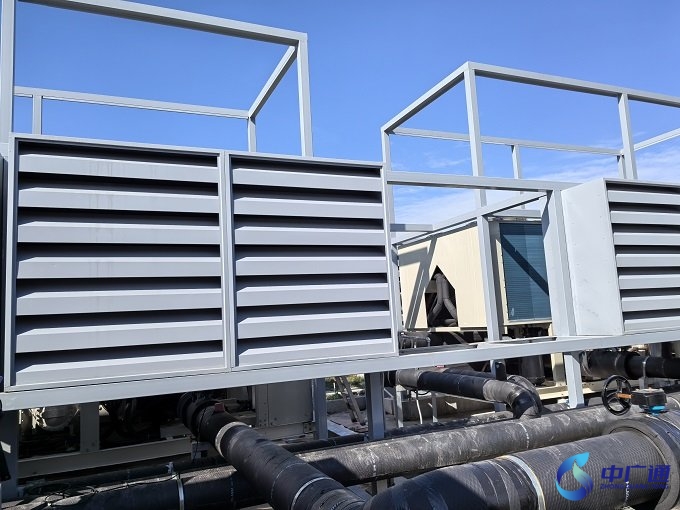
一、噪聲源分類及特征
1. 空氣動力性噪聲(主要來源)
- 典型設備:風機、壓縮機、透平機、空冷器、鍋爐、氣體/蒸汽放空口。
- 成因:氣體高速流動、湍流、噴射或壓力突變引起。
- 特點:聲壓級高(>90 dB)、傳播距離遠,疊加效應顯著。
2. 機械性噪聲
- 典型設備:機泵、電機、傳動設備、空氣錘。
- 成因:機械摩擦、振動、撞擊或高速旋轉。
- 特點:中高頻為主,易通過結構傳遞至周邊環境。
3. 電磁性噪聲
- 典型設備:變壓器、大功率電機。
- 成因:磁場振動誘發鐵芯疊片共振。
- 特點:低頻噪聲穿透性強,治理難度高。
4. 管道及閥門噪聲
- 典型設備:高壓氣(汽)管線、節流閥、文丘里管。
- 成因:介質高速流動、湍流、節流壓降。
- 特點:沿管線傳播,易形成線狀噪聲污染源。
二、噪聲治理關鍵技術方案
1. 消聲技術
- 適用場景:氣體動力噪聲(壓縮機、風機進出口、放空口)。
- 措施:安裝阻性或抗性消聲器(如空冷器頂部消聲器、小孔噴注消聲器)。優化放空口設計(多孔擴散消聲結構)。
2. 隔聲技術
- 適用場景:高噪聲設備(壓縮機房、電動機、加熱爐)。
- 措施:機房墻體采用吸隔聲復合結構(如金屬隔聲板+巖棉填充層)。設備加裝隔聲罩(半封閉式或全封閉式,需兼顧散熱需求)。設置聲屏障(空冷器周邊,兼顧通風與降噪)。
3. 吸聲技術
- 適用場景:室內混響噪聲控制(壓縮機房、操作室)。
- 措施:墻面安裝吸聲材料(如穿孔鋁板+玻璃棉吸聲結構)。
4. 阻尼減振技術
- 適用場景:機械振動噪聲(機泵、管道、閥門)。
- 措施:設備基礎加裝減振器(彈簧/橡膠隔振墊)。管道包裹阻尼材料(如約束層阻尼涂料+隔聲氈)。
5. 工藝優化
- 適用場景:流體噪聲(管道、閥門)。
- 措施:降低介質流速(優化管道直徑與流速設計)。采用低噪聲閥門(多級降壓結構)。
三、治理難點與關鍵設計原則
1. 多源疊加效應
- 挑戰:露天裝置區噪聲源數量多、分布廣,需分區分級治理。
- 策略:優先控制主導聲源(如空冷器、放空口)。建立聲場模型預測疊加效應,優化降噪方案。
2. 設備功能性需求平衡
- 核心矛盾:降噪措施需兼容設備運行特性。
- 解決方案:隔聲罩設計預留散熱通道(如消聲百葉窗)。巡檢口采用可拆卸隔聲模塊,便于維護。
3. 極端工況適應性
- 挑戰:高溫、腐蝕性環境(如加熱爐、蒸汽管線)。
- 材料選擇:耐高溫吸聲材料(陶瓷纖維棉)。防腐蝕隔聲結構(不銹鋼外殼+氟碳涂層)。
4. 長期可靠性
- 關鍵點:避免降噪設施因振動、老化失效。
- 措施:動態設備(風機、壓縮機)采用柔性連接。定期監測隔聲結構密封性。
四、典型案例效果評估
設備類型 | 治理前噪聲級(dB) | 治理措施 | 治理后噪聲級(dB) | 降噪量 |
---|
壓縮機房 | 105~110 | 吸隔聲墻體+消聲器+隔聲門 | 80~85 | 20~25 |
空冷器 | 95~100 | 聲屏障+頂部消聲器 | 75~80 | 20 |
高壓放空口 | 110~120 | 小孔噴注消聲器 | 85~90 | 25~30 |
管道閥門 | 90~95 | 阻尼包扎+低噪聲閥門 | 75~80 | 15 |
五、結論與建議
- 綜合治理:需結合源頭控制、傳播路徑阻斷及受體保護(如操作室隔聲)。
- 智能監測:部署聲學傳感器網絡,實時監控噪聲變化并優化治理策略。
- 全生命周期管理:從設備選型階段介入(優選低噪聲型號),避免后期改造成本過高。
通過系統性降噪設計,石油石化企業可顯著改善作業環境(崗位噪聲≤85 dB),同時減少對周邊社區的聲污染投訴風險(廠界噪聲≤65 dB)。